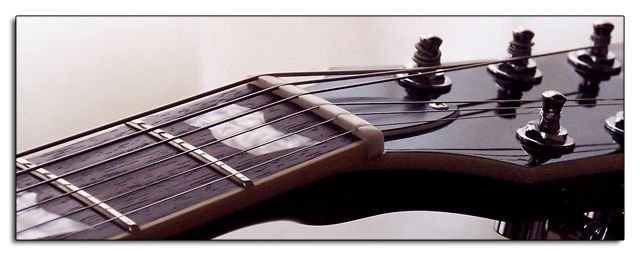
In this article we will see the different types of nut for electric guitar, and their different characteristics. This small component of the guitar is often forgotten, even by the guitar manufacturers themselves, especially if it is a low-cost instrument. Since the meticulous adjustments that a nut requires will raise the cost of the guitar.
A large part of amateur and professional guitarists, the first thing they usually throw away from their new guitar is the nut, for one nut made by hand and perfectly adjusted by a luthier.
Only in high-end guitars, more attention is paid to the nut to obtain its maximum benefits, but they are usually very expensive guitars.
This does not mean that we have to change the nut of our electric guitar tomorrow. But it is a matter to take into account as the first improvement of our instrument. For example, before changing pickups, it doesn’t hurt to change the nut first.
How to Adjust a Guitar Nut
If we decide to change the nut due to a break, or to change the material it is made from, we have to check the measurements very well, and the most efficient and safest thing to do would be to buy two identical nuts.
We sanded the lower part of one nut, and after checking that no open strings buzz, we sanded the other nut a little more to try to optimize the fit.
After checking that there are no buzz, we can adjust the former nut a bit more. If one of the nuts finally causes some kind of buzz by playing the open strings, we will already know that the nut that remains alive has the perfect setting.
Shape of the Lower Part of the Nut
This would be in the event that the nut to be changed had a flat bottom. If the bottom of the nut had an arched shape, something very common in Fender models, things get quite complicated. In this case it would be better to buy a nut with the same curvature, and reset the grooves to optimize its fit, if necessary.
Remove of the Nut Guitar
Another issue would be to remove the nut installed as standard, without dramatic consequences. There are some that do not offer much resistance, but others on the other hand, are conscientiously attached, and their removal would be somewhat difficult even for a professional. Although a luthier has the necessary tools for these high-risk issues.
In any case, if you make the decision to remove it yourself, I will tell you that at least you will have to pass a cutter around the nut, to cut the varnish that may have stuck to it. This way the varnish will not jump when removing this component from the guitar.
In any case, there are also nuts designed so that the height of the strings can be modified, such as the ABM 6210 Webster model. But as we already know, before making a purchase we must review the measurements.
The same previous method can also be applied to adjust the height of acoustic guitar saddles. Since this piece usually comes standard at an excessive height by decree.
I do not recommend the creation of a nut entirely by the inexperienced. Since a luthier has the necessary tools and experience for its adjustment and perfect settlement on the neck. If the nut does not have maximum contact with it, it will not adequately transfer the vibrations of the strings.
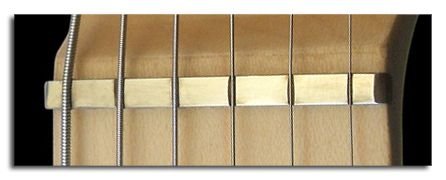
In addition, the placement of a nut by an expert is not usually too expensive, except for those made of bronze, as it is a more complex material to work with. But they offer an excellent result in terms of tone, durability and finish.
A nut requires a perfect fit. If the grooves on the strings are too deep, the strings buzzling when played open. And if they are too high it will make it difficult to handle the instrument.
Guitar Nut Materials
Another issue would be the construction material of the nut, generally found in plastic materials in series guitars.
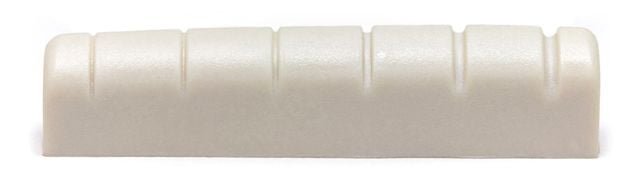
These materials resemble the characteristics of bone, but of course…, it is not the same, simply because they are different materials. Even the bone should be from an animal of a certain age with the bones fully developed and calcified, and not from a young animal.
Many think that this is not so important, because the nut would only affect the notes when we play them open. But that is not true…, since the nut influences the total sound of the instrument, by absorbing the vibrations of the strings at all times and transmitting them to the neck.
This would be more noticeable with a bronze nut, with bronze offering a distinctly brighter hue than other materials.
Graphtech
We can also find electric guitar nuts made of synthetic materials, specially designed for the sliding of the strings through the grooves of the nut, such as Graphite or Graphtech. The latter is composed of graphite mixed with Teflon, to obtain a greater glide.
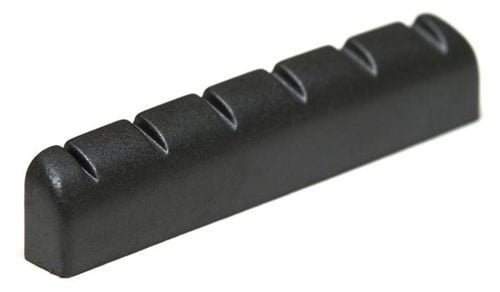
This is very useful when it comes to maintaining the tuning of the instrument after performing a bend, and for the use of semi-floating bridges. Obtaining the maximum performance of this type of bridge, with this style of nuts accompanied by locking tuning pegs. Since the tremolo bridge loosens the strings, and the locking tuners will prevent any possible slippage.
Bone is not as slippery as these materials, but the solution is to lubricate the grooves of the nut with lubricants such as Micro Teflon, or Nut Sauce.
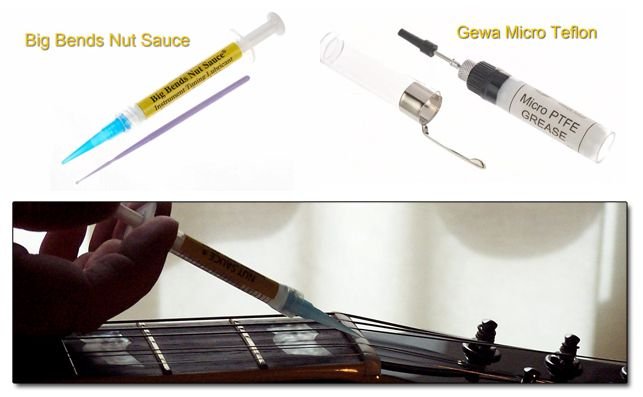
In metal nuts for electric guitar, we can find bearings to facilitate this sliding, as in the Fender LSR roller nut.

To completely avoid the problem of strings slipping through the nut grooves, we have locking nuts that mount Floyd Rose style bridges. In this way the matter is completely settled, by blocking the strings to the nut once in tune. Then we will adjust the tuning of the guitar through the fine tuners of the bridge.
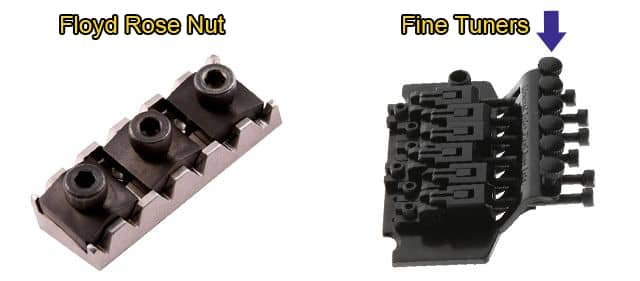