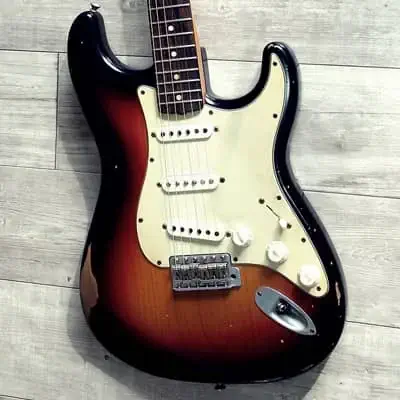
The most used guitar finishes are:
- Oils and Waxes
- Shellac
- Nitrocellulose
- Polyurethane
Guitar Finishes with Oils and Waxes
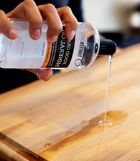
Waxes and oils have always been used to treat wood, and it is one of the oldest methods used for its protection and beautification.
And although it would be the method that offers the least protection compared to other types of finishes, it is highly appreciated in general, given its naturalness and warmth to the touch, and it is mainly used in the treatment of guitar necks.
The treatment with oil and wax is such a distinguished finish that prestigious brands such as Music Man use it widely in the final treatment of the wood of the neck, as in the case that appears in the image below.
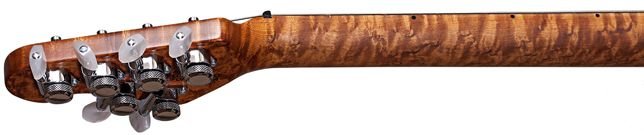
The darkened color of this neck is not due to this treatment. It is a toasting applied to the wood that is very characteristic of the brand, before the final finish with oil and wax.
Since I’m talking about Music Man, I want to clarify that the brand normally uses polyurethane for the body finishes of its instruments, and dispenses with materials as charismatic as the ultra-famous nitrocellulose. Although we will talk about these materials in detail later.
Application of Oils and Waxes
Going back to the topic of oil and wax treatments, unlike other finishes this one would need some maintenance as we would need to reapply new coats of oil and wax as time and use progressed. But enjoying a neck with this finish and touch is really worth it.
If we like natural finishes, this finish can also be used on the body of the guitar, when it is completely free of varnish.
This method is easier to apply than other finishes with paints or varnishes, we will obtain an optimal result manually, and without the need for special tools or protective equipment. Since both oil and wax are non-toxic natural products, which we can apply with a cloth.
Whenever we do something for the first time, we should do it with some measure. And although it is something very simple to apply, it is not a question of bathing the guitar in oil either. Therefore, we must always take the precaution of stretching the materials very well, and apply little by little in several layers until the desired finish is obtained.
Tung Oil and Beeswax or Carnauba Wax
Different oils for wood can be used, which we can find in most specialized stores. Although one of the most used is 100% natural Tung oil for quality and price.
For DIY lovers, I will tell you that we can use this type of oil to hydrate and beautify any type of wood. This way we will avoid the use of synthetic products.
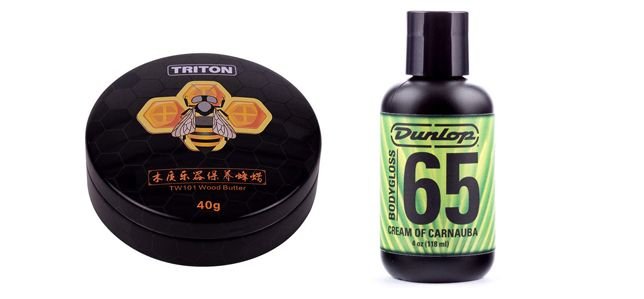
As for the most used waxes, there is beeswax and carnauba wax. This material will finish covering the pore and polish the wood, and we will obtain the softness and slight satin shine that satisfactorily culminates our work.
Guitar Finishes: Shellac
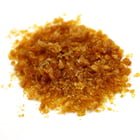
Another of the natural materials most used in guitar finishes would be shellac. Natural resin obtained from the secretion of the lacquer cochineal, used mainly in instruments with a sound box such as acoustic guitars.
This treatment has always been preferred by master guitarists in the manufacture of classical instruments, due to its lightness, crystallization and shine. This material is much more laborious and complex to apply compared to oil and wax.
Guitar Finishes: Nitrocellulose
Instead, during the decades of the 50s and 60s, the pioneers in the development of the electric guitar such as Fender and Gibson opted for the mythologized nitrocellulose, for the finish of their instruments. Semi-synthetic material that can finish a guitar in a very thin layer, allowing the wood to resonate and breathe more easily.
This would be fine for an acoustic instrument, but for an instrument that does not have a soundboard, is amplified, and is generally distorted, it may not be as relevant. Especially if we weigh all the elements of the guitar equipment that can also (or even more significantly) influence the final sound of the instrument.
Fame of Nitrocellulose
Personally I am convinced that the main fame of what is known as nitro lies in the fact that the most legendary models of both Fender and Gibson were built with this type of resin. We can possibly find more tonal variations between different string gauges, not to mention different types of pickups and amps.
In what would be the issue of tone and sonority, I would worry more about the general quality of the instrument, than its finish. Since the main functions of this are to beautify and protect the instrument from external elements, mainly humidity.
In addition, there would be many drawbacks associated with the use of nitrocellulose, since it usually fails precisely in the main qualities and characteristics that a good finish must offer us, such as resistance to shock and the passage of time.
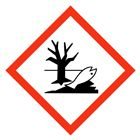
Nitro is usually applied with a spray, and given its high toxicity, we will have to apply it in a well-ventilated environment with a protective mask.
As a result of the environmental dangers derived from this material, its use and commercialization is beginning to be prohibited in some areas such as California.
Guitar Finishes: Polyurethane
Consequently, nitrocellulose has been replaced in the construction of electric guitars today in a general way by polyurethane, both in low-cost and high-end guitars. A less toxic synthetic material, with faster drying, a more intense and lasting shine, and offers greater protection given its high resistance.
Another advantage of using this material compared to nitrocellulose is that it better preserves the color of our guitar. Since nitrocellulose acquires a yellowish tone with the passage of time.
Disadvantages of the Nitro Finish, Compared to Poly
Also, nitro deteriorates much faster than polyurethane, and has the characteristic tendency to chip and crack. Although ironically many think that this is precisely what makes a beautiful beautiful guitar.
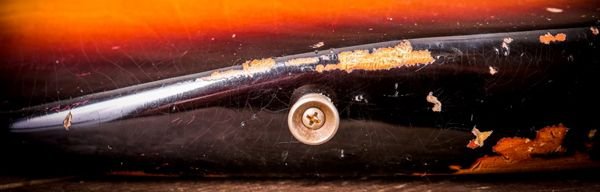
As if all this were not enough, some components of the old and legendary nitrocellulose have ceased to be manufactured, and new additives have been added that have made it, for too long, especially sticky when our hands sweat, with the extreme discomfort that this can entail.
Wait there’s still more. The nitro is also sensitive to certain plastic materials, and it can deteriorate if we place our guitar on stands that are not suitable for this type of finish.
Final Conclusions
So today, possibly a thin layer of polyurethane is the most advisable as a finish for an electric guitar. Although if we want the finish of our guitar to interfere as little as possible with the final sound of our electric guitar, I would opt for oil and wax. Since it is the treatment that can least interfere with the free vibration of the wood.
Some will think that the best thing will be to keep the wood natural and the matter settled. But a guitar without any type of treatment is more exposed to changes in humidity that can affect its structure, and consequently cause expansions that could affect the adjustment of the instrument. Something that in the worst case can cause deformations, or even crack the wood.